Research
1.Surface tension measurement of high temperature metallic melt using electromagnetic levitation
Numerical simulation is widely used to improve and optimize manufacturing processes for various high value-added high temperature products through melt solidification, such as high reliability welding of reactor vessels and the precision casting of turbine blades for airplanes. For simulating a heat/mass transport process involving a free surface of molten metals, an accurate surface tension and its temperature coefficient of the melt is strongly required to consider the effect of Marangoni convection.
In our laboratory, surface tension of molten metals is measured by oscillating droplet method using electromagnetic levitation technique. This technique enables us to measure the surface tension of molten metals over a wide temperature range including the undercooling condition. This is attributed to the sample not being in contact with the container, which is chemically reactive with the sample at high temperatures and plays a role in the nucleation site below the melting point. An extension of temperature range of the measurement would result in a reduction in the uncertainty of the measurement for the temperature coefficient. This technique can also assure the control of oxygen partial pressure of measurement atmosphere because a glass tube for atmosphere control can be employed within a coil.
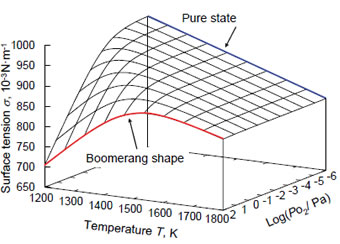
Fig. 3 Surface tension of molten silver as functions of temperature and oxygen partial pressure. The boomerang shape temperature dependence of surface tension due to oxygen adsorption/desorption is successfully observed.
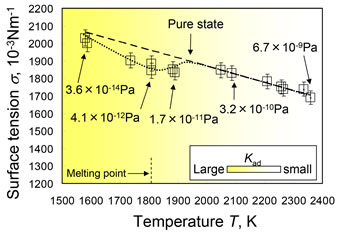
Fig. 4 Surface tension of molten iron measured under reducing gas atmosphere. The kink in temperature dependence of the surface tension was discovered under a reducing gas atmosphere, which is attributed to the competition between temperature dependence of equilibrium constant of oxygen adsorption reaction, Kad, and that of oxygen partial pressure of reducing gas
2. Precision measurement of thermophysical properties of molten metals under microgravity.
When the EML technique is applied under microgravity conditions, the surface tension of the levitated droplet can be calculated from its single surface oscillation of the l = 2 mode known as the Rayleigh oscillation. Surface tension,σ, of molten metals can be calculated from the following Rayleigh equation,
where M is the sample mass and ν is the frequency of the Rayleigh oscillation. On the ground however, the frequency of the l = 2 mode splits into three corresponding to the m = 0, }1, and }2 oscillations, because the droplet is deformed from a sphere to an oblate spheroid by gravitational acceleration and electromagnetic forces from the levitation coil. As a result the theoretically-derived Cummings and Blackburn calibration is required for the explaining the effect of the deformation of the droplet. Several research groups measured the surface tension of molten metals using an EML under microgravity condition to prove the validity of the Cummings and Blackburn calibration. However the oxygen partial pressure of atmospheric gas was not controlled and measured in those studies.
We attempt to measure surface tension in consideration of the effect of the oxygen partial pressure of atmospheric gas under microgravity condition during the parabolic flight of an airplane to confirm the validity of the Cummings and Blackburn calibration. Furthermore the measurement at international space station (ISS) is in preparation to permit the more precise measurement.
3. Development of new material processing under ultra low oxygen partial pressure
In order to suppress an oxidation of material during various material processes such as casting, annealing, and sintering, reducing gas atmosphere of H2 and CO is often employed. However these gases cannot always be employed in practical industrial manufacturing because it is dangerous substance. Furthermore, chemical reactivity of these gases and produced materials must be considered. In order to reduce oxygen partial pressure of atmospheric gas during various materials processing, stabilized zirconia is used as an oxygen pump in our laboratory. The purpose of this study is to develop new materials and new material processes.
4. Exploration of new metastable phase by undercooling solidification using containerless process
In the containerless technique such as EML, the levitated droplet often cools down far below the equilibrium melting temperature in the liquid state prior to solidification because of the absence of container wall that may act as heterogeneous nucleation sites. This phenomenon is called undercooling. When molten alloy is solidified from deep undercooling condition, a new metastable phase may be crystallized. In our laboratory, we explore a new metastable phase using the containerless technique to develop a various functional materials such as high performance magnet and semiconductor